|
|
Quality Workforce Leads To Quality Products |
As a trusted consumer brand in many households, a factory in Shah Alam believed that when the workforce is well-trained and assessed consistently, effective skills transfer will take place and the standardised work practices will ensure the quality of its products.
This was why this factory began its journey in developing Competency Based Training (CBT). In 2004, they selected CEDR Corporate Consulting (then known as S.I.T Corporate Learning Centre) for its experience in setting up training and assessment systems, to do a pilot project with one of their departments.
First Milestone: Pilot CBT project
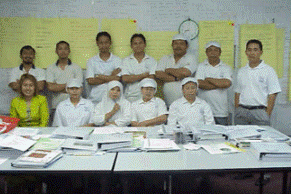
The pilot project team
For the pilot project, a group of senior operators were taken off the production line for more than 3 months. This team was assigned to learn how to develop task breakdown and assessment tools as well as how to train and assess other operators. All these activities were new to them and it created some anxiety amongst them.
Knowing their fears and reservations, the CEDR trainers adapted the training, coaching and practical sessions to their level. With the assistance from a temporary clerk and continuous support from the management, the team members persevered in their preparation of the training and assessment documents. They also overcame their initial stage fright when conducting training and assessment.
Implementing the CBT System
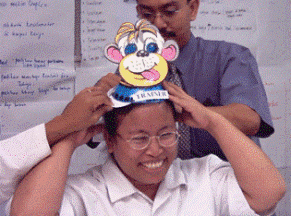
CEDR training session with pilot project team
Following the positive signs from the pilot project, 3 team members from the pilot project were selected to form a special group. Instead of operating the machines at the production floor, they were given a new role in their department – as full-time CBT trainers and assessors.
From then on, task breakdowns and assessment tools for different types of machines were developed. Conducting training sessions and assessments for the operators became routine tasks for this special group. They set up the initial CBT records system and ensured that the department workforce was competent.
Due to the encouraging results in the first department, the other departments in the factory also started their CBT projects with CEDR.
CBT and ISO Certification
In 2008, the factory decided to replace their work instructions with the task breakdown (pictorial work instructions) and to include the assessment tools as part of their documentation for ISO. Each department was required to update/ review the task breakdowns and assessment tools periodically for the on-going audits.
In addition to that, new operators were required to complete the CBT training and assessment within 6 months, with the assessment checklist being used as a supporting document for confirmation. Besides involving the senior operators, this factory also recognised the role of their frontline managers in monitoring the CBT system in their respective departments and engaged CEDR to train them accordingly. At the same time, a training executive was hired for the specific role of aligning and standardising the CBT implementation in all departments as well as ensuring that all CBT documents in digital format were securely stored.
CBT Accelerates TPM Implementation
When the factory began to implement Total Productive Maintenance (TPM) in 2009, the CBT task breakdown came in handy. Due to the availability of detailed task breakdowns, they were able to skip a time-consuming step – line mapping for the processes and therefore speeded up their implementation of TPM.
With the task breakdown as reference, corrective action required at the production floor could be identified and reassigned to the operators (after they had been trained to do so). The faster response time by operators would then translate into a longer meantime between failure and better control of losses.
Integration of CBT with Quality Systems and Career Pathways
CEDR has trained a number of Subject Matter Experts in this factory and other companies. It is noteworthy that no other factory or company has integrated the CBT with their other systems e.g. quality systems/ initiatives such as ISO, as thoroughly as this factory.
The job of an operator in this factory has evolved with the growing demands of their industry. A few years ago, a new category of operators (at a new job grade) was created. This new category of operators is responsible for not only the operation of the assigned machine but also for the basic maintenance of the machine. CBT manuals were developed by fitters for the training and assessment of this new category of operators. In the near future, this category of operators will be trained to be CBT trainers and assessors in their department. CBT has become an important area of involvement for operators who want to move on to the next level of their career in this factory.
Benefits of CBT Integrated with Other Systems
The integration of CBT with other systems, be it quality systems or performance management systems in a company will definitely increase the impact of training and assessment on the company’s operations. It is when training and assessment are implemented in isolation from the other initiatives in the company that the impact is sometimes not seen.
Training and assessment are not meant to be an end in itself, i.e. it is not the ‘destination’. However, training and assessment can be powerful ‘enablers’ or ‘pathways’ for a company to reach their goal of producing quality products. |
(This article was written by CEDR in the spirit of Knowledge Sharing; to share CEDR’s experience with companies outside the Lion Group for the benefit of the Lion Group companies.) |
|
|